Below you can find a list of the most frequently asked questions that are asked to us by those who enter the world of sandblasting, if you do not find what you are looking for click here to contact our Customer Service or to access the online troubleshooting.
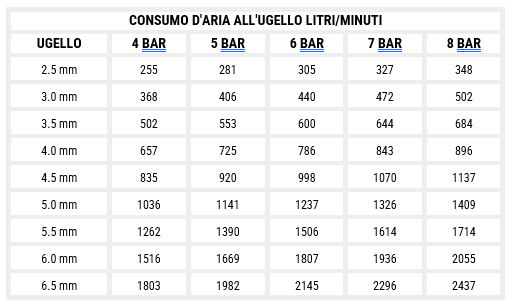
There is a substantial difference. A reverse-pressure system, or an aspiration system, uses the Venturi principle which allows the sand to be suctioned into a container and mixed with compressed air. The reverse-pressure system pushes the air and abrasive down, projecting a mix of these substances as one solution; the resulting jet is far more powerful when compared to the Venturi system (for example, with the Sabix, Pressure Blaster).
In the sandblasting machine section, you will find our corresponding products, as well as others.
The only difference is the type of inert substance (abrasive material) that is used with the machine. Bead blasting refers to treatment using glass, ceramic, steel, etc. types of microspheres. Sandblasting refers to treat using sharp-edged abrasives (sand, aluminum oxide, garnet, etc).
Hourly consumption depends on various factors. For a realistic calculation, it is necessary to know the diameter of the nozzle, exerted pressure, type of abrasive, type of surface (brick, wood, metal, hard stone, marble, etc.), and type of treatment (satin finishing, finishing, carving, restoration, stripping) Consumption can be anywhere from 10 kg/hour to beyond 200 kg/hour.
For free jet sandblasting, the user must protect his or her face, respiratory pathways, and wear a protective suit.
For suction blasting, eye and ear protection is sufficient.
Sandblasting becomes pollutive when the user does not consider the type of abrasive that should be used or the resulting dust during jobs. The primary concern is the resulting dust, which can be removed by using a humidifier or aerohydro blaster. In contrast, this problem does not exist in the case of suction blasting.
Thanks to aerohydro sandblasting and humidifier systems, it is possible to carry out blasting without dust, guaranteeing the user the power to carry out treatments in public, historic centers, and outdoor environments.
With the use of glass, di ceramic, and steel microspheres the user can achieve a process that doesn't alter or create coarseness on surfaces. In summary, it is important to use a round-edged abrasive that doesn't remove the material.
There is no fixed distance that should be maintained from surfaces being treated. This can depend on various factors.
- Type of material being treated
- Type of desired results
- Type of inert substances
- Exerted pressure of sandblaster
- Diameter of nozzle
Practical example:
Sabix (free jet pressure sandblaster), 3 mm nozzle,
4 bar pressure,
garnet mineral abrasive,
brick restoration: approximate distance of 10 cm.
The main are the following - each has a different purpose:
coriblast,
steel blast,
garblast,
quarzite,
microlux,
dust lux,
eco blast,
bic blast,
cerablast